CNC Compression Tooling, lets talk about them…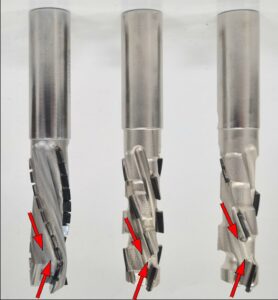
There a many different types of cutting tools available for machining wood based materials, composites and laminates. As such the choices can be overwhelming.
Straight bits, up-cut, down-cut, compression. HSS (High Speed Steel), TCT (Tungsten Carbide tipped), STC (Solid Tungsten Carbide) and PCD (Polycrystalline Diamond). Which one do you choose?
CNC Compression Tooling Types
Each type has their place with associated advantages and disadvantages. Here we will explain the differences in more detail.
The most common style of tools used in engineering for the machining and drilling of metals has the flutes ground in an up-cut spiral pattern. The angle of the spiral, or helix, varies. This depends on the type of metal the tool was designed to cut. And the number of flutes.
Conventional end mills are up-cut, the spiral cutting action of the tool forces the chips up and out of the cut.
Why use Compression Tooling?
Thin materials like plywood tend to be pulled up and this may distort the cut making it inaccurate. The up-cut action of the tool tends to leave rough edges on the top side of wood based materials. This being more pronounced on Melamine faced panels as the Melamine coating is quite brittle.
Although, in the case of wood based materials, the up-cut action aids extraction of the chips on CNC routing machines.
Conversely, a down-cut spiral tool tends to push the workpiece down on to the machine table. Great for keeping the panel firmly clamped. However, the disadvantage is that the chips are also being forced downwards into the cut. This makes extraction of the chips more challenging. With possible clogging of the tool.
Machining a double sided Melamine faced panel (MFC) with an up-cut tool achieves a good finish to the bottom edge of the panel. While the top edge of the board will have a poorer finish. With fibres pulled upwards and chipping out of the Melamine coating. This may be acceptable if the rough edge is not visible. Generally both sides of the panel will be on show and this is where the Compression tooling helps.
What compression tool do I need?
CNC Compression tooling is available in a variety of styles and budgets. To suit a variety of industries such as small joinery shops to large Kitchen and Bedroom furniture manufacturers.
Prima Tooling Ltd manufactures compression tooling in solid carbide and PCD (Polycrystalline Diamond) tipped. Including a variety of configurations available from stock.
Solid Carbide
Most Solid Carbide Spiral compression tools used in woodworking are either 1, 2, or 3 flutes. With either a standard length up-cut of around 10-12mm for general work and thicker workpieces. Alternatively with a short up-cut portion of the tool for nesting operations or very thin materials.
PCD Tipped
Our range of PCD tipped compression tooling is manufactured as Z=1+1, Z=2+2, Z=3+3 and Z=3. Generally, the more tips, the faster your feed rate can be, in short more PCD tips, more expensive.
A compression tool is basically an up-cut and down-cut in one tool. The flutes go one way at the bottom of the tool and the opposite way at the top of the flute.
Compression cutters are used on materials such as Melamine faced panels, wood veneer, plywood, composites and laminates.
Due to the design of the tool. Chips are pulled towards the middle of the tool. Therefore, eliminating the chipping to the top and bottom of the panel. Resulting in a clean edge on both sides. Also helping reduce de-laminating.
Solid Carbide and PCD tools can be custom made to suit any application. Whilst a conventional compression cutter will be a longer down-cut portion of the flute. Some tools are manufactured with a long up-cut and short down-cut for improved performance.
Not all tools are created equal.
Undoubtedly there will be price differences with tools from other manufacturers that look identical. Solid Carbide comes in various grades of hardness. Understanding that cheap tools will invariably be made with a low quality grade of Carbide, and manufactured as quickly as possible.
A quality designed and engineered tool will last longer and perform better. Hence, be prepared for the higher price tag.
PCD tooling is no different. A lower price for a similar looking tool will most probably be due to a reduced area of the PCD tip.
Over the lifetime of the tool the initially cheaper tool can work out costly. Due to having to replace tips sooner.
As PCD tools can only be sharpened by reducing the cutting diameter every time. The re-sharpenable area of the PCD is an important factor when considering tooling costs.