Compression Tooling
There a many different types of cutting tools available for machining wood based materials, composites and laminates, and the choices can be overwhelming.
Straight bits, up-cut, down-cut, compression. HSS (High Speed Steel), TCT (Tungsten Carbide tipped), STC (Solid Tungsten Carbide) and PCD (Polycrystalline Diamond).
Each type has their place with associated advantages and disadvantages, so we will try to explain the differences in more detail.
Read all about compression tooling here!
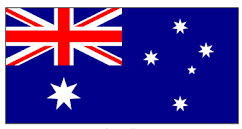
Our Router tooling is reaching far and wide.
With over 40 years in manufacturing we have supplied tooling to many different countries. In 2019 we saw sales to Japan, Malta, Indonesia among a few.
However we are very excited to welcome on board our newest distributor in Melbourne, Australia though...exciting times ahead!
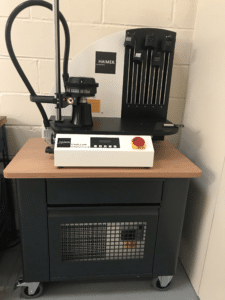
Why you need Shrink Fit Technology
How often do you review your tool holding? time is money right? so machine down time or setting time should be kept to a minimum for maximum efficiency...
You may consider using a shrink fit tool holder rather than a conventional collett? At Prima Tooling we are able to fit new tooling into Shrink fit holders, as well as service tooling by removing the router tool and refitting it into the shrink fit collett before returning the serviced tool to our customer, included in the price of our service.
We often find ourselves giving advice to customers who are experiencing poor cutting quality, short lifespan of tooling, excessive noise or even tool breakage, we usually find that this is due to the wear and age of the tool holder.
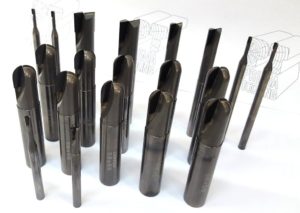
PCD tooling for High Speed Milling, are you machining MMC's, O-CMC's, CFRP or Non-Ferrous materials?
Our PCD tipped End Mills have been in use since 2008 by Aerospace, Automotive and Engineering companies not only in the UK, but around the world!
Used for machining non-ferrous materials like Metal Matrix Composites (MMC), Oxide Ceramic Matrix Composites (O-CMC),
Copper and Brass, non-metallic materials such as Carbon Fiber Reinforced Plastic (CFRP)
Glass Fiber Reinforced Plastic (GFRP), Glare®, Graphite, Model board and other highly abrasive materials.
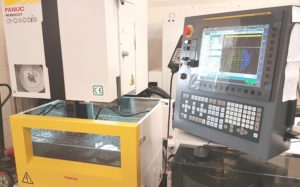
Meet the newest member of the team!
Latest news! Our new Fanuc Robocut 4 axis wire EDM, installed and cutting PCD discs into standard size PCD tips and custom profile pieces for our PCD tipped Router tools. Much quicker than our old Agie machines and extra capacity for other types of work.
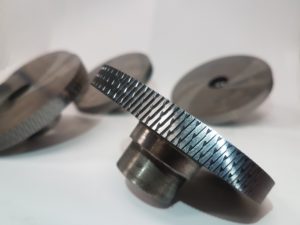
Something other than Router Tooling...
Something different this week, one of our customers sent in some Solid Tungsten Carbide weld seam removal discs for regrinding.
The discs have a minimum size, so we were able to reduce the diameter and cylindrically grind off the wear before grinding some nice new shiny teeth.
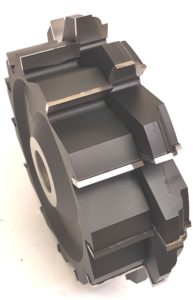
Every day brings something different at Prima Tooling
Repeat order for a pair of 2 part, Tungsten Carbide tipped profile sets we recently manufactured,
250mm OD x 73 cut width.
These tools are used for milling the profile end mullion on PVC aluminium window and door frames.
Just one of many industries we manufacture cutting tools for!
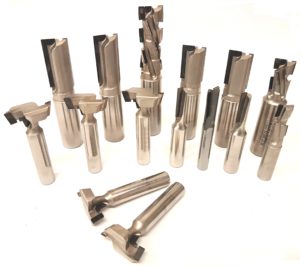
It's like a Diamond tool family...
Its great to see some of Prima Tooling's PCD Router family together! this is just a small selection of PCD tipped router cutters for machining wood based products such as MDF and MFC.
PCD Slatwall, PCD compression and PCD straight tooling are all available in custom designs or standard sizes from our wide range of PCD tooling stock, with stock sizes available for next day delivery.
Manufactured in Britain... what's not to like!
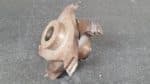
Hello again after 26 years!...

Prima Tooling still working with old school tool sharpening.
Old school sharpening of TCT tooling on our Jones and Shipman Tool & Cutter grinder.
This machine is probably older than me, but it is still more than capable of grinding a variety
of new and service Tungsten Carbide cutting tools, from profile spindle tooling to router cutters and drills.
We offer a full service in Tungsten Carbide tools, from manufacture to sharpening and repairs to complete re-tipping if required.
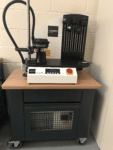
Prima Tooling continue to invest and develop new services
Our Shrink fit machine is installed and ready to add another area of work to our current PCD - Diamond and TCT - Carbide tool servicing.
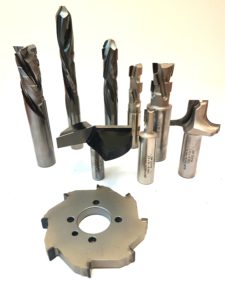
Interested in trialling our tooling?
We are always happy for any potential customers to trial our British Made PCD Router and Spindle tooling to see how it compares to what they currently use... we are confident that the quality of tooling from Sutton tools will speak for themselves...
Are you using Router Tooling to cut think foam?
Prima Tooling are delighted to launch our new product range!
Should you be talking about using HSS spiral tooling for cutting foam? Would you like a better finish with your machining? We have a solution...
Prima Tooling Ltd's HSS 4 flute Spiral Router Tooling can answer both of those questions and possibly more.
As a UK tooling manufacturer we are always looking at new materials and how we can adapt our manufacturing to suit the current tooling requirements, as well as maintaining our core business values which we have held for over 40 years.
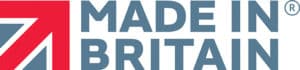
British Made PCD and Carbide Router and Spindle Tooling
Our Linked in post has had over 11,000 views which has been incredible.
'As a nation united against the current enemy and fearful of the immediate future, there has never been a better time to support UK manufacturing.
We are well aware that in the coming months, years maybe there will be an uphill struggle for many UK Business to save costs. So I am sure the temptation to shop overseas for cheaper alternatives will be looked into, and continued for those that currently do.